George Weston Foods, Baking Division is the company behind some of NZ’s best-loved brands. These include Tip Top®, Bürgen®, Golden, Big Ben® and Ploughmans® Bakery.
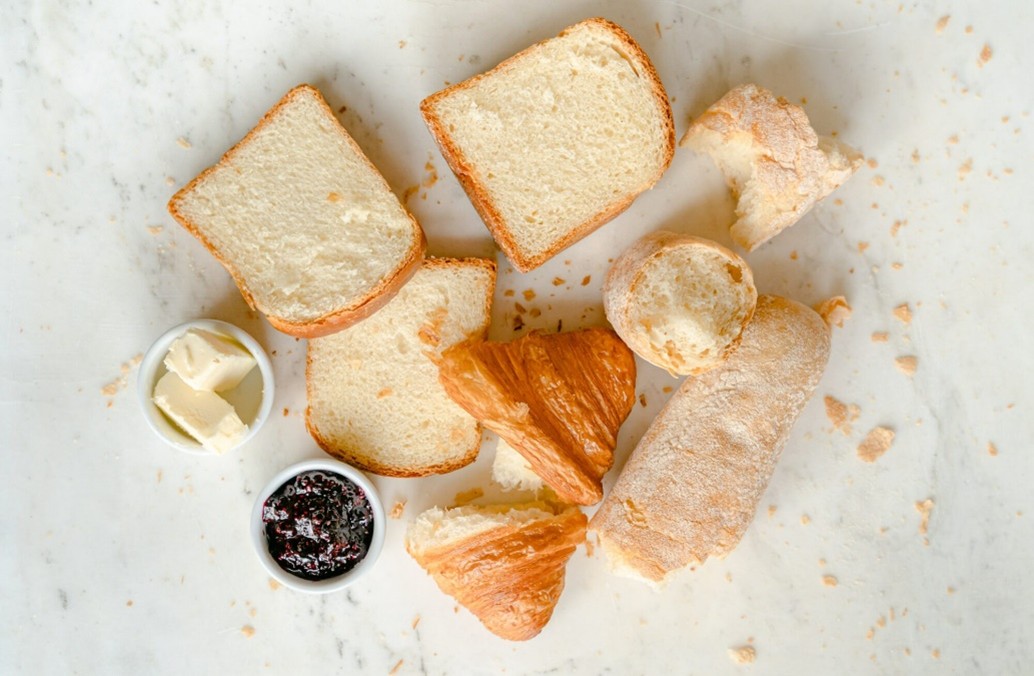
CHALLENGE
The Baking Division at George Weston Foods needed a solution to manage breadcrumb waste in their production area without causing additional mess or conveyor track issues. The company required a conveyor system that could handle crumbs efficiently while maintaining cleanliness and safety.
SOLUTION
EQM Industrial provided an N-Track conveyor system with sidewall belting designed to prevent breadcrumbs from spilling onto the floor or into the conveyor itself. This minimized hygiene concerns and ensured a safe work environment. The N-Track system is simple in design, was easy to install and was delivered semi-assembled. This allowed George Weston Foods’ engineers to complete the installation.
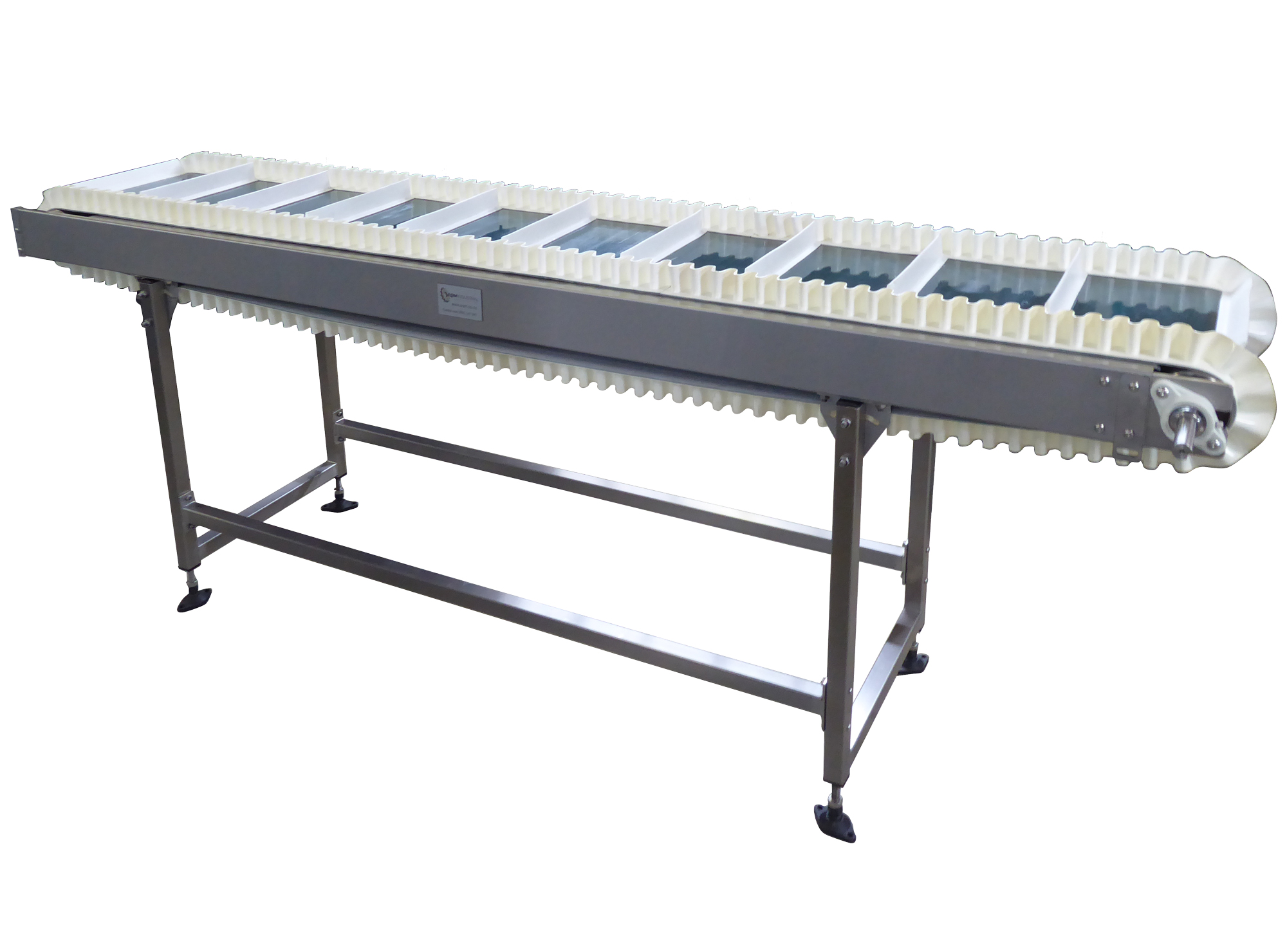
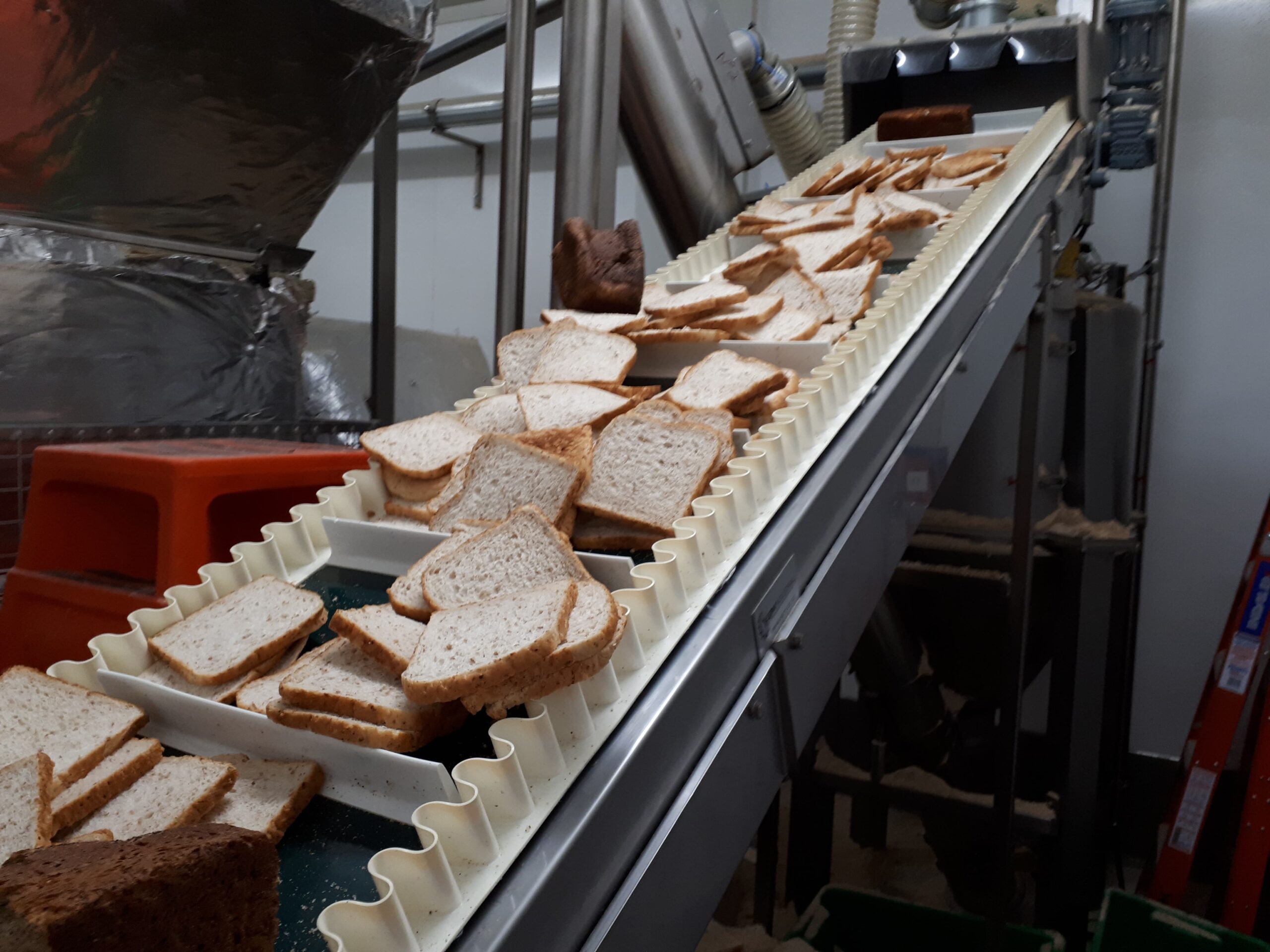
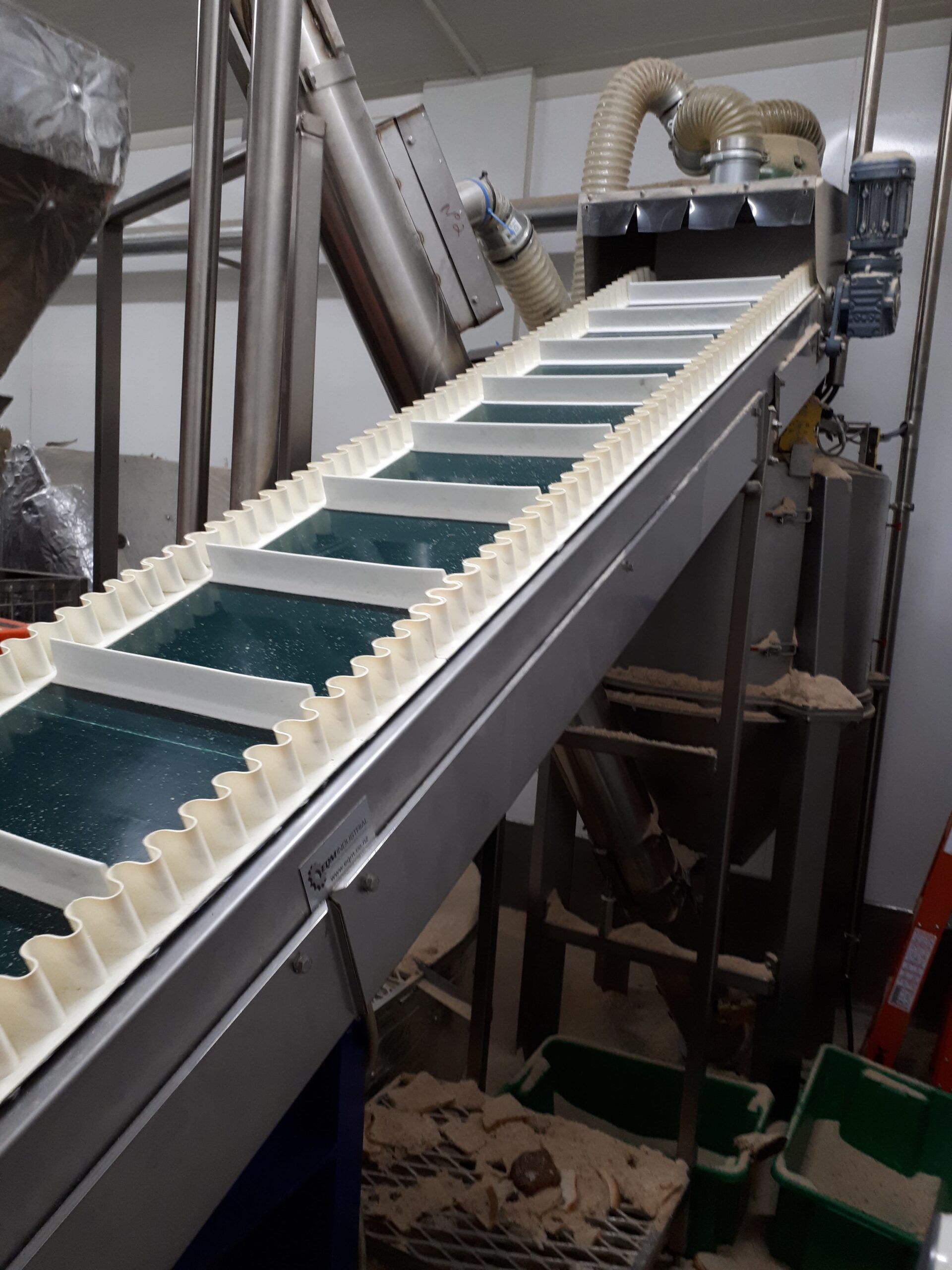
BENEFITS
- Prevented breadcrumb spills, reducing mess and improving hygiene
- Fast delivery and installation, with the system up and running in just three weeks
- Cost-effective solution with a straightforward design
- Enhanced operational efficiency by addressing waste management directly
Contact us for a solution to increase productivity on your production line today. Benefit from our knowledge, expertise and experience.
Better by Design.